Innovative Robotic Solutions
Enhancing efficiency and safety with advanced robotic arms for various industrial applications and cleaning systems.
Robotic Arm Solutions
1. Industrial Robotic Arms
Ensuring Safety and Operational Excellence
Conduct Risk Assessments – Perform hazard evaluations in line with ISO 10218 and ISO/TS 15066 before deployment.
Implement Collaborative Robotics (Cobots) – Use force-limiting sensors, emergency stop functions, and safety-rated monitoring for human-robot collaboration.
Maintain Regular Service Schedules – Lubricate joints, inspect wiring, and calibrate sensors to avoid downtime and mechanical failures.
Secure Robotic Programming – Protect controllers from cyber threats through network segmentation, firmware updates, and user access control.
Train Operators Thoroughly – Ensure all personnel are proficient in safety protocols, operational procedures, and emergency responses.
2. Industrial Cleaning Systems
Maximizing Cleaning Efficiency and Worker Safety
Deploy Automated Cleaning Solutions – Utilize robotic scrubbers and vacuums with advanced navigation and obstacle detection.
Ensure Chemical Safety – Use non-toxic, biodegradable cleaning agents and equip workers with appropriate PPE.
Implement Preventive Maintenance – Routinely clean nozzles, replace filters, and monitor battery performance.
Comply with Hygiene Standards – Adhere to OSHA guidelines and ISO 14644 cleanroom regulations where applicable.
Adopt Smart Cleaning Technology – Leverage IoT and data analytics to monitor cleanliness levels and optimize cleaning schedules.
3. Industrial 3D Printing (Additive Manufacturing)
Promoting Quality Control and Workplace Safety
Store Materials Properly – Keep filaments and powders in humidity-controlled environments to maintain material integrity.
Calibrate and Test Frequently – Perform regular calibration of print beds, extruders, and lasers to ensure print precision.
Prioritize Air Quality and Safety – Use HEPA filtration for hazardous emissions and provide PPE such as respirators and gloves.
Protect Digital Assets – Secure CAD files and printing systems with encryption and isolated network access to prevent tampering.
Refine Through Post-Processing – Apply techniques like heat treatments, polishing, and surface finishing to enhance durability and product quality.
Cross-Industry Best Practices
1. Predictive Maintenance – Use AI/ML algorithms to forecast equipment failures and schedule proactive repairs.
2. Optimize for Energy Efficiency – Streamline robotic paths, cleaning routines, and print settings to reduce energy consumption and material waste.
3. Ensure Regulatory Compliance – Follow ISO, ANSI, and OSHA standards applicable to each process and system.
4. Invest in Continuous Training – Upskill workers regularly on emerging technologies, safety measures, and compliance standards.
Conclusion
Integrating advanced automation, rigorous safety measures, and proactive maintenance strategies allows industries to achieve higher productivity with reduced operational risks across robotics, cleaning systems, and 3D printing.
Innovate with care. Operate with precision. Succeed with safety.
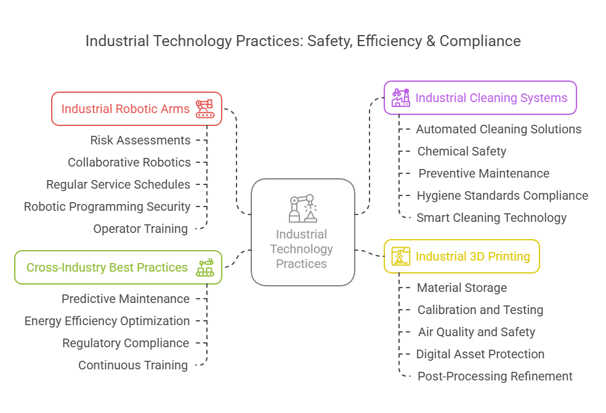
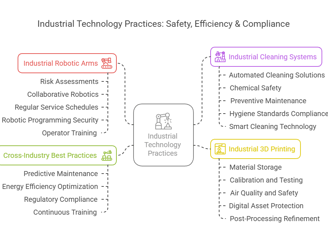
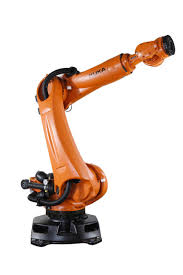
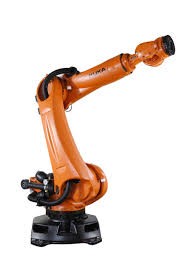
Contact Us
Reach out for inquiries about our robotic arms and safety solutions. We're here to assist you.
Get in touch
83 Watsonbrook Dr. Brampton, L6R 0R5, ON, Canada
contact@aidoctrine.com
Shahed Tower, 10 Floor, Mirgab, Kuwait city, Kuwait